Understanding Remote I/O: It's Functions, Benefits, Applications
Everything you need to know about remote I/O and its importance for industrial automation.
What is remote I/O? They are a flexible, cost-effective and reliable solution for detecting and controlling signals in industrial automation. They enable I/O modules to be installed decentrally, thus reducing cabling and simplifying installation and maintenance.
Importance and definition of remote I/O
Remote I/O, or RIO, short for remote input/output, is a system with which various sensors and actuators can be connected at decentralised locations within a plant or network and their data can be managed via a central controller. Nowadays, remote I/O is an essential part of modern automation solutions, as it supports the flexible integration and scalable expansion of automation networks. This is particularly important in complex industrial environments in order to efficiently manage all the necessary processes. By integrating remote I/O, industrial control systems can be changed and extended more flexibly without the need to make major changes to infrastructure. By using remote I/O, companies can reduce their operating costs, increase efficiency and simplify maintenance. Close cooperation with central control units and communication protocols such as PROFINET, EtherCAT® or Ethernet/IP is crucial for reliable data transfer and system performance.
How remote I/O works
- I/O modules: these modules record the signals from sensors (e.g. temperature or pressure sensors) and control actuators (e.g. valves, motors). There are different types of I/O modules, including analogue and digital, depending on the type of signals that have to be processed.
- Communication interface: the recorded signals are transmitted via a communication interface (e.g. PROFINET, EtherCAT® or Ethernet/IP) to the central controller, e.g. a PLC (programmable logic controller). This interface enables bidirectional communication between the remote I/O modules and the central controller.
- Bus coupler: the bus coupler connects the I/O modules to the industrial network. It handles communication between the individual modules and the central control unit.
Benefits of remote I/O

- Since they are extremely flexible and scalable, companies can easily expand and customise their networks. This is particularly important in dynamic industrial processes, as it makes it much easier to respond quickly and efficiently to changing requirements.
- High cabling and installation costs can be reduced.
- Easy to install and maintain.
- Reliable data transfer thanks to modern communication protocols such as PROFINET, EtherCAT® or Ethernet/IP. These protocols provide a fast and
secure data flow between the various components of an automation system, thereby increasing the performance and reliability of the overall system.
What is the difference between local and remote I/O?
A local or central I/O is installed in the control cabinet together with the PLC. A remote I/O, on the other hand, is decentralised and installed separately from the control unit.
The choice between deciding on a local I/O or remote I/O depends heavily on the individual requirements and framework conditions of an application, e.g. a centralised architecture may make sense in smaller systems, while larger, more complex networks may benefit from the strong points of a decentralised structure. Another aspect that companies should consider is compatibility and integration with existing controller systems to guarantee seamless and efficient implementation.
What is decentralised I/O?
Decentralised I/O is a remote I/O system with a predefined number of inputs and outputs. It is a self-contained unit and cannot be expanded.
Applications
Remote I/O is used in a wide range of industrial and process automation systems to reduce the amount of wiring required. In the chemical and pharmaceutical industries, remote I/O systems enable production processes to be precisely monitored, thus contributing to compliance with strict safety and quality standards. Remote I/O is used in the energy and utilities industry for operating power stations, water treatment plants and distribution networks. It is also used in the automotive industry in larger applications such as production lines and robot cells. Ultimately, the possible applications of remote I/O are as diverse as the requirements of the various industries, which only further emphasises its importance for modern automation solutions.
*note: this blog was provided by Festo, view the original here
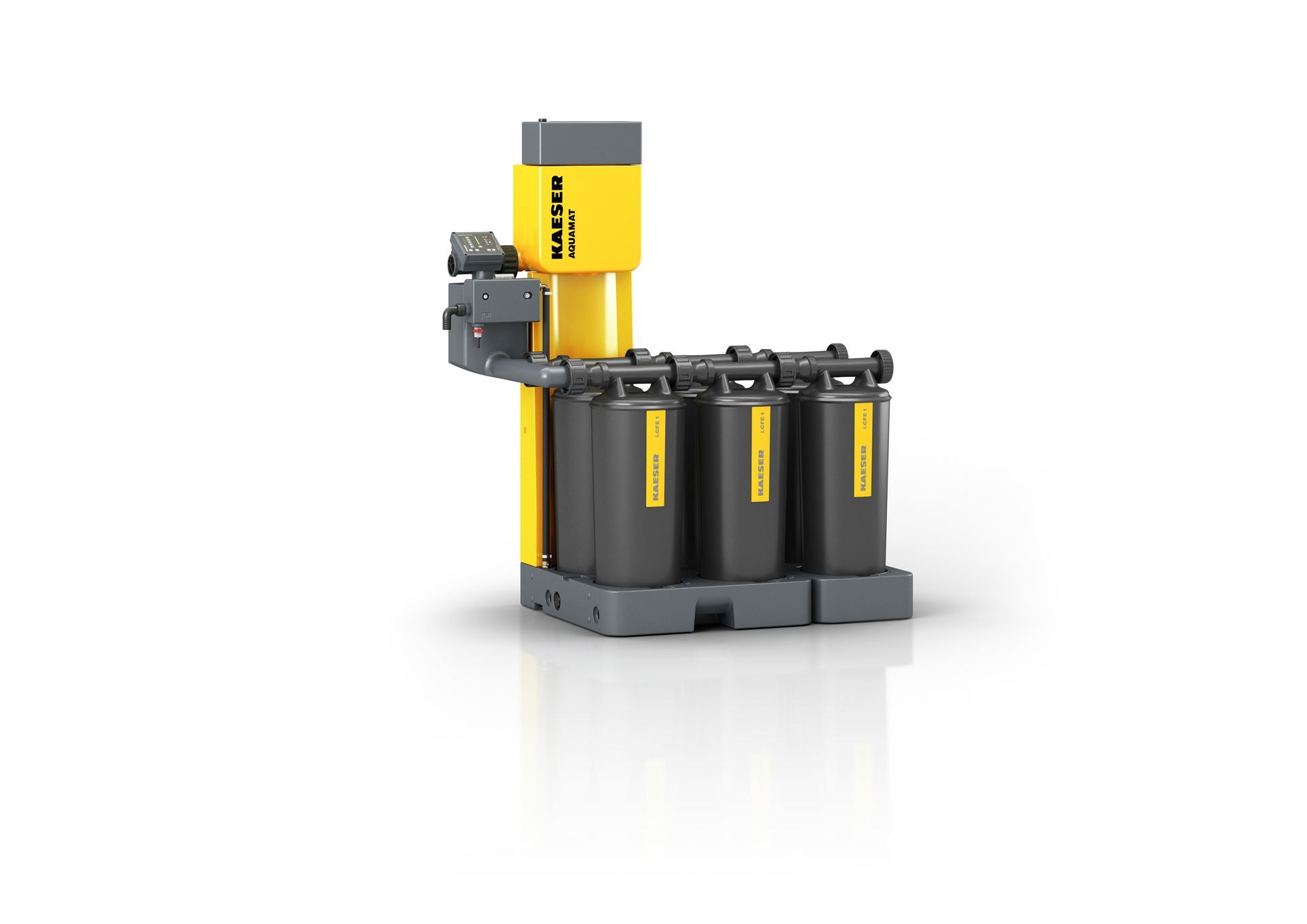
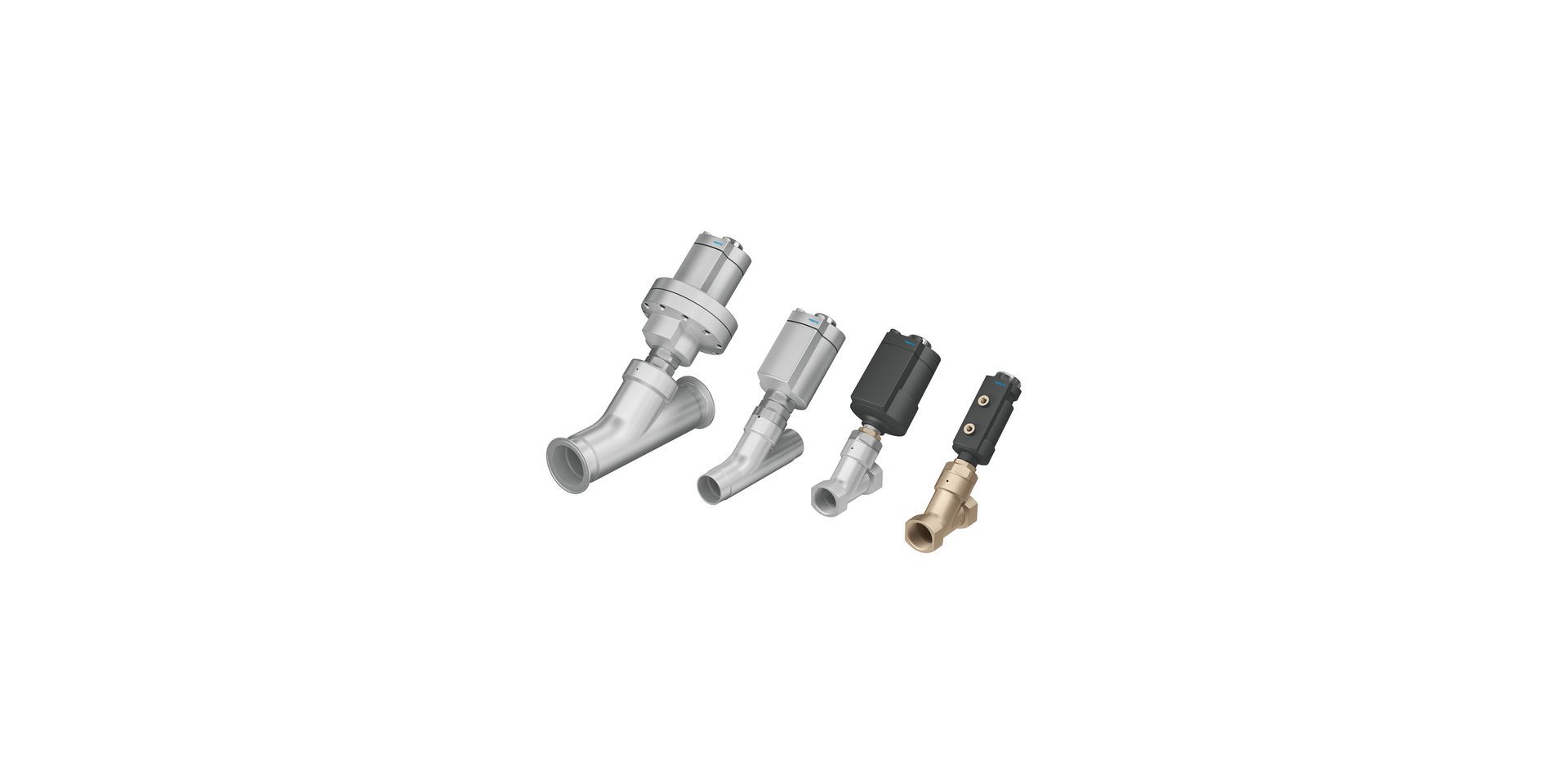
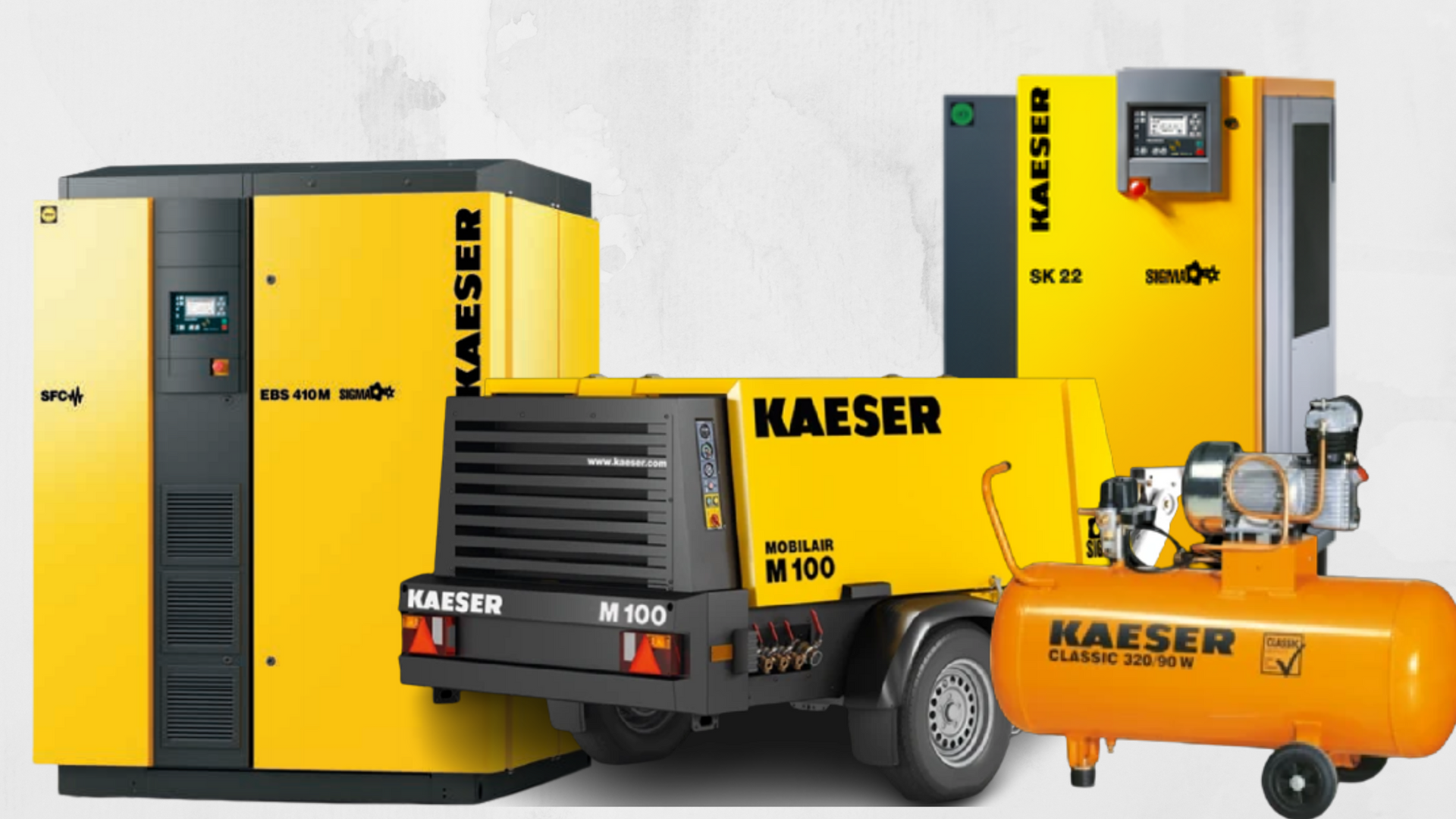
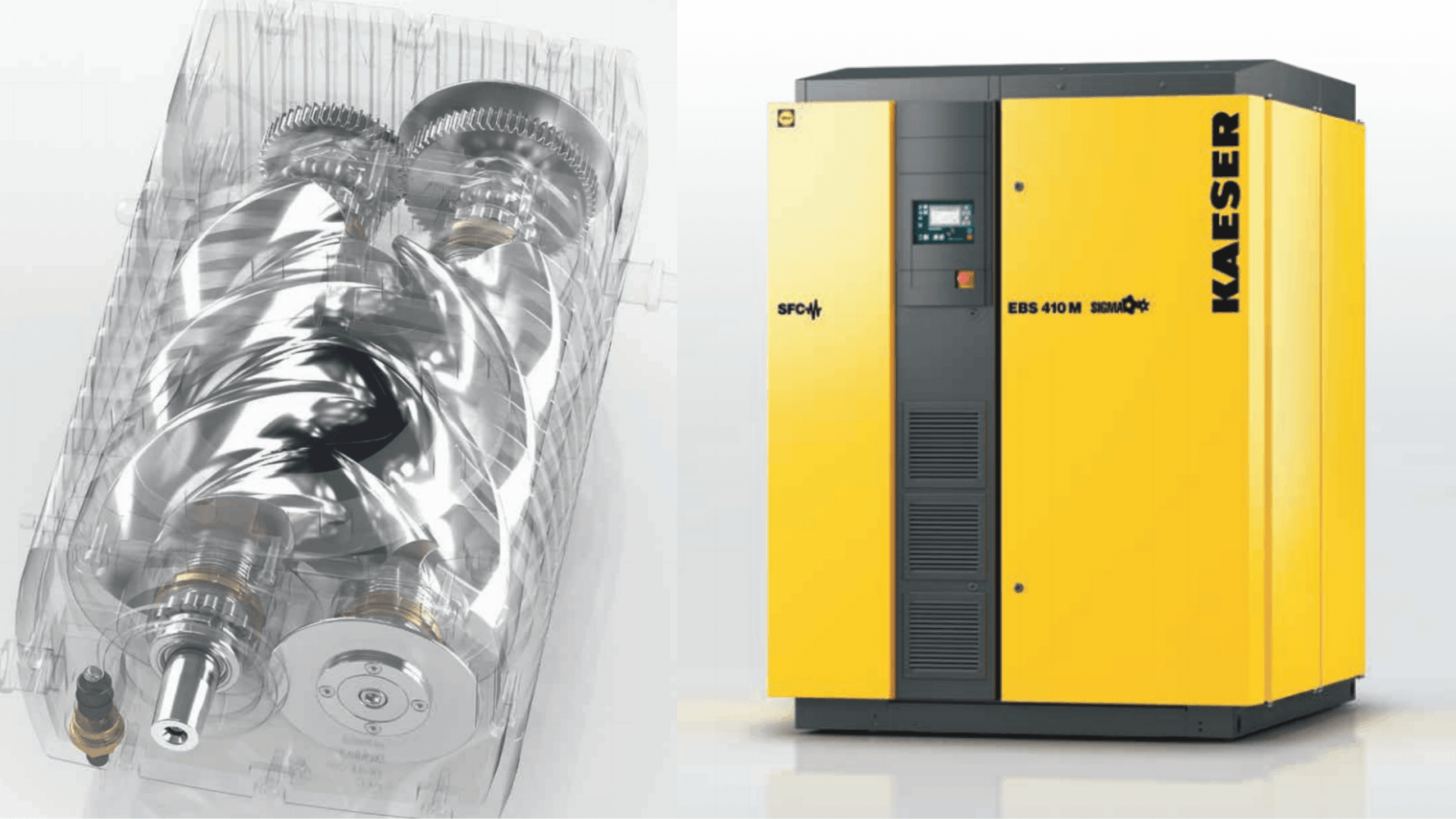
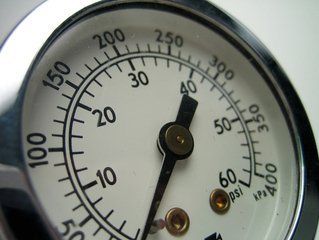